Establishing sustainable way to recycle GRINDING SLUDGE.
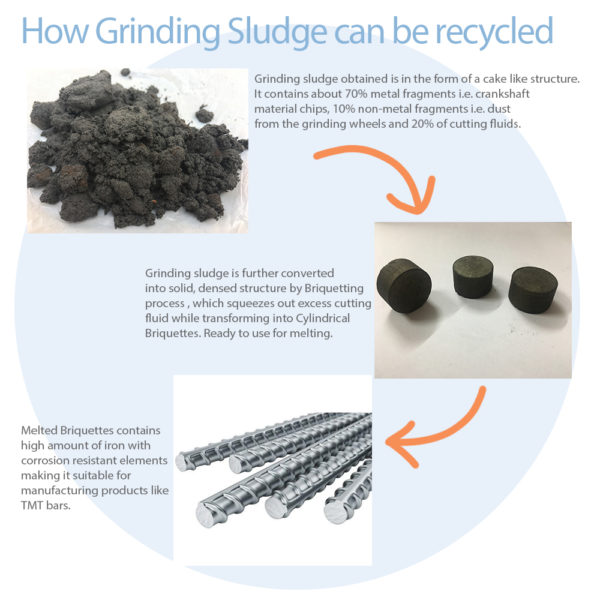
This project deals with exploring the potential application of an industrial by-product/waste called ‘Grinding sludge’ by efficient recycling.
How Grinding Sludge is generated?
Grinding machine utilises expensive cutting wheel (CBN) and cutting fluid (emulsion to reduce friction at the cutting zone) to obtain precision parameters on the component. The cutting action results in the removal of material from the component in the size of microns and negligible amounts of abrasives from the wheel due to wear. The coolant carries these extracted materials from the machine to the filtration unit where maximum amount of coolant is filtered by vacuum filtration process. The filtered coolant is recirculated to the machine and hence reused. The extracted material that gets accumulated on the filter paper is the ‘Grinding sludge’ which has a wet and caked consistency.
Grinding Sludge - Composition
Grinding sludge contains 70% extracted metal fragments (alloy steels), 25% coolant and 5% non metal fragments from CBN wheel. Contains 94% of Iron along with other elements, hence proving to be valuable.
A by-product awaits 'productive disposal'
It was classified in the industrial waste category till date, but is now being rightly termed as 'by-product'; as it is categorised as hazardous material of our process it is even more compulsively asks for "productive disposal".
Recycling Solution - Briquetting Process
Grinding sludge needs to be converted into a solid, densified structure so as to be feasible for melting. It can be done by compressing the sludge at a high pressure in a press i.e. Briquetting. The process squeezes out excess cutting fluids while transforming the metal chips into compact, easy-to-manage cylindrical metal briqs . The oil extracted during the process can be reused again. Metal briqs so formed are 99% free from oils. Briqs can now be melted and hence recycled.
Applications
Melted briquettes contains high amounts of iron along with corrosion resistant elements (Cr+P+Cu) in adequate amounts.
High carbon content can be reduced by using slag refiners and low carbon scraps while melting.
Composition makes it suitable for manufacturing products like Thermo mechanically treated (TMT) bars.
DISCLAIMER: The project and concept is privileged, making copies, reproduction and publication without written consent of Srinivas Induction Hardening is strictly prohibited.